La transition numérique en cours dans la plupart des secteurs révolutionne les pratiques du monde industriel. Celui-ci deviendra l’industrie 4.0, ultraconnectée, bardée de capteurs, capable de s’adapter seule à un grand nombre de modifications ou de perturbations, et permettant ainsi plus d’agilité et de fiabilité. C’est d’autant plus le cas pour l’industrie nucléaire, industrie de haute technologie et dont les exigences de sûreté sont incomparables. L’utilisation de la réalité virtuelle et l’apparition de maquettes numériques des bâtiments et des processus deviendront ainsi des alliés indispensables pour la formation des personnels, permettant une maîtrise des risques associés à toute activité nucléaire.
Sûreté et compétitivité : la formation au cœur de la filière nucléaire
La filière nucléaire est la 3e filière industrielle française. Elle représente environ 220 000 emplois directs non délocalisables. La part de la formation dans le chiffre d’affaires est 3 fois plus élevée que la moyenne nationale de l’industrie, ce qui correspond en moyenne à 9 jours/an pour les employés, qu’il s’agisse de formations initiales ou de remises à niveau de leurs habilitations. En effet, la filière doit maintenir les connaissances clés nécessaires à l’utilisation contrôlée et sûre de la production d’énergie nucléaire, et assurer le renouvellement des compétences vers les jeunes générations.
L’État, conscient de ces enjeux, a lancé un appel à projets en 2021 sur le « Renforcement des compétences de la filière nucléaire ». Il s’agit d’une part d’adresser les enjeux de la sûreté nucléaire, qui nécessite une main-d’œuvre qualifiée et spécialisée devant intégrer très tôt les gestes et les comportements liés à la sûreté. Cela repose sur la conscience des risques et suppose des réactions appropriées, efficaces et intelligentes en toutes circonstances. D’autre part, dans une industrie mondialisée où la transition numérique est en marche, la formation se doit de soutenir les enjeux de compétitivité et de maîtrise des coûts. L’ingénierie nucléaire doit ainsi affronter de vrais défis avec de nouvelles méthodes de travail plus collaboratives et la mise en œuvre de technologies complexes et innovantes, dans des chantiers d’envergure.
La réalité virtuelle, vers plus d’efficacité
La réalité virtuelle est une réponse à ces enjeux. En privilégiant la pratique dans un contexte « pseudo-réel », elle permet un transfert direct des situations industrielles réelles et des savoir-faire technologiques, et in fine des gains de temps, de productivité et d’efficacité.
Vos dons donnent de la voix aux chercheur•euses.
Faire un don
Les avantages principaux de la réalité virtuelle pour la formation professionnelle sont la possibilité de réaliser des tâches en toute sécurité, de permettre de refaire les gestes industriels, de créer des scénarios pédagogiques dans des conditions rares, comme des accidents. Pour l’industrie nucléaire, il s’agit par exemple d’accéder au cœur d’un réacteur nucléaire ou de former les travailleurs à des interventions impossibles à reproduire dans la réalité, par exemple un changement de joint défectueux en zone hautement radioactive.
Au CNAM par exemple, la réalité virtuelle est utilisée en parallèle des cours magistraux de physique des réacteurs en permettant aux élèves de se déplacer dans les parties inaccessibles du cœur. Les travaux pratiques de mesures nucléaires ont quant à eux été totalement virtualisés, pour permettre aux élèves de s’entraîner à leur guise en suivant des scénarios pédagogiques. Leur déroulement s’effectue de manière individuelle et collective, soit en présentiel (avec un casque de réalité virtuelle), soit à distance (avec un ordinateur). Enfin, grâce aux dernières évolutions des technologies de réalité virtuelle, une salle virtuelle multi-activités a été créée, donnant la possibilité totalement innovante aux apprentis et enseignants d’interagir en partageant du contenu, tel que des devoirs, des échanges oraux ou des cours.
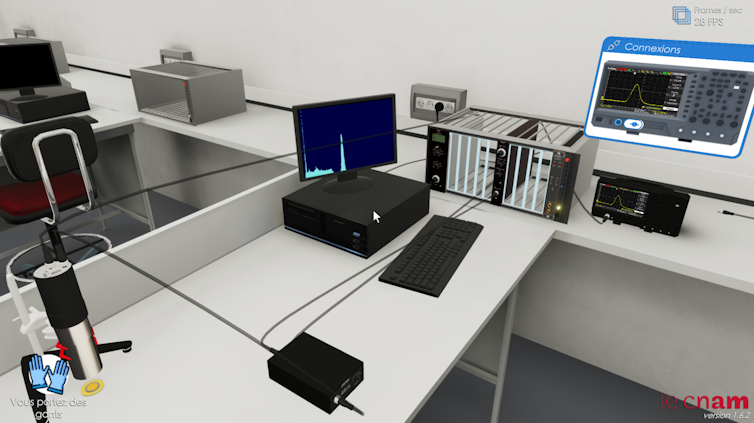
En réalité virtuelle, tous les sens sont atteints, permettant ainsi une compréhension plus aisée des phénomènes et une meilleure intégration des gestes techniques. Cette technologie est encore nouvelle et peu d’études sont encore menées. Néanmoins les premiers résultats sont encourageants.
L’évaluation précise et scientifique des bénéfices de la réalité virtuelle pour la formation est encore à trouver. De nombreuses méthodes sont proposées et il sera important de trouver les bons critères d’évaluation. Les traces numériques laissées par les élèves (temps d’hésitation, nombres d’essais ou d’erreurs…) pourront aider à trouver des critères objectifs pour évaluer l’apport de la réalité virtuelle en formation.
Le jumeau numérique dans la filière nucléaire
La filière nucléaire va encore plus loin dans sa volonté d’évolution numérique de ses projets. L’idée est désormais de concevoir, exploiter, maintenir et déconstruire à l’aide des jumeaux numériques, c’est-à-dire un ensemble de programmes informatiques interconnectés modélisant une infrastructure – une centrale nucléaire par exemple – et son comportement sur l’ensemble de son cycle de vie.
Le concept de jumeau numérique dans l’industrie ressemble à ce qui se fait en construction et architecture avec le BIM, appelé aussi « maquette numérique du bâtiment ». Dans ce domaine, la maquette numérique est en fait le prototype du bâtiment et donne des informations sur sa géométrie, ses matériaux et ses installations techniques (l’emplacement exact des conduites d’eau, par exemple).
Une installation nucléaire est complexe. D’une part, les procédés industriels (production de chaleur par la radioactivité, transport de la chaleur, comportement des fluides et matériaux, chimie du recyclage…) sont nombreux. D’autre part, une installation nucléaire représente plus de 50 bâtiments, plus de 150 systèmes élémentaires comme une ventilation ou une pompe, plus de 500 trémies ou plus de 2000 kilomètres de câbles. Le tout doit être géré sur une durée d’environ 100 ans, de la conception à la déconstruction. Il est donc fondamental de conserver la mémoire de l’ensemble des données de l’installation à tout instant (référentiels sûreté, matériaux, données sur le comportement des systèmes ou issues des capteurs sur site, essais…). Pour mémoriser, organiser et prioriser ces flux de données, le jumeau numérique (donc un clone de l’installation à un instant t) doit donc être associé à une plate-forme de gestion des données (en anglais Product Lifecycle Management ou PLM).
Mais le suivi des infrastructures et des procédés n’est pas le seul intérêt des jumeaux numériques. En intégrant la réalité virtuelle, ces clones participent également à la formation de l’ensemble des corps de métiers ayant besoin d’intervenir sur les installations nucléaires. Toutes les interventions pourront ainsi être jouées autant de fois que cela sera nécessaire, afin de supprimer toute hésitation le jour où elles seront réalisées en conditions réelles.
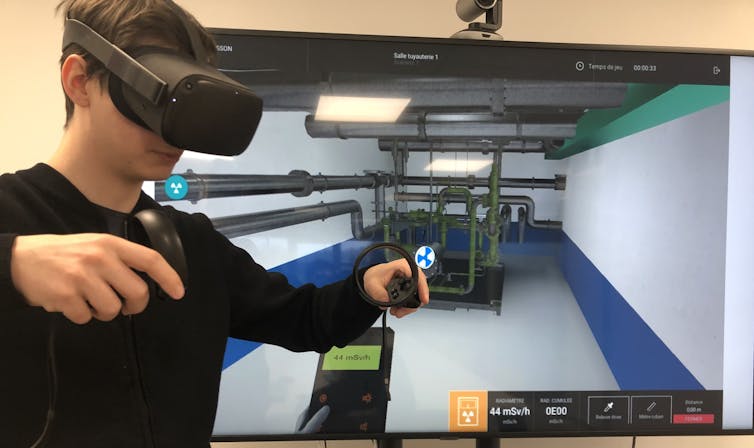
Un des projets de jumeau numérique de la filière nucléaire est celui du « Réacteur numérique ». Le but affiché est de créer « un réacteur nucléaire couvrant les phases de conception, d’exploitation et de déconstruction, en fonctionnement normal, incidentel ou accidentel ». Ce projet bénéficie d’un budget de 30 millions d’euros et environ 200 personnes travailleront dessus pendant 4 ans. D’autres installations nucléaires, telles qu’une usine de retraitement, le projet d’enfouissement des déchets nucléaires CIGEO, ou le projet ITER pour la fusion nucléaire sont eux aussi en train de construire leur propre jumeau numérique.
La filière française espère ainsi gagner sur deux aspects : la sûreté et la compétitivité. C’est la formation de tous les métiers grâce à la réalité virtuelle et le jumeau numérique qui permettra d’optimiser le fonctionnement des réacteurs dans la durée, d’améliorer la qualité des interventions et de gagner en performance industrielle.
Deux défis attendent les acteurs de la digitalisation des installations nucléaires. Le premier est l’interopérabilité des simulations numériques (appelées aussi codes de calcul), de la physique au niveau microscopique (simulation neutronique, thermohydraulique… du cœur du réacteur où se développe la réaction en chaine de fission) jusqu’au niveau macroscopique géométrique des bâtiments. Les échelles prises en compte dans les codes de calculs sont différentes, tout comme les langages informatiques et les formats de données. Il faudra donc créer une plate-forme de couplage informatique, où tous les codes de calculs pourront communiquer et opérer ensemble. Le second défi est la gestion optimisée des données issues de l’installation sur tout le cycle de vie de l’installation. Le choix d’une plate-forme PLM adaptée et sécurisée sera primordial. Pour la déconstruction des installations nucléaires, un projet européen a même été mis en place pour harmoniser ces aspects.
Si la filière nucléaire réussit ces challenges, le fonctionnement des installations nucléaires en temps réel sera accessible sur un simple ordinateur de bureau, via évidemment des protocoles et des liaisons hautement sécurisées.
Emmanuelle Galichet
Enseignante chercheure en physique nucléaire, Conservatoire national des arts et métiers (CNAM)
Cet article est republié à partir de The Conversation sous licence Creative Commons. Lire l’article original.